Exploring the Intricacies of Lithium Battery Production
In an increasingly electrified world, lithium batteries have become indispensable power sources, driving everything from smartphones to electric vehicles. Understanding how these batteries are made unveils the complexity behind their seemingly simple design. This article delves into the intricacies of lithium battery production, shedding light on the processes involved from raw materials to final assembly.
Raw Materials
Lithium batteries rely on a careful selection of raw materials, each contributing to the battery's performance, safety, and longevity.
Lithium Compounds:
l Lithium carbonate and lithium hydroxide are primary lithium compounds used in battery production.
l These compounds serve as the source of lithium ions in the battery's electrolyte, crucial for its electrochemical reactions.
Electrolytes:
l Electrolytes are essential for facilitating the movement of lithium ions between the battery's electrodes during charging and discharging cycles.
l Common electrolyte formulations include lithium salts such as lithium hexafluorophosphate (LiPF6) dissolved in organic solvents like ethylene carbonate (EC) and dimethyl carbonate (DMC).
l Solid-state electrolytes are also under development, offering potential advantages in safety and energy density.
Cathode Materials:
l Cathode materials determine the battery's voltage, energy density, and stability.
l Common cathode materials include lithium cobalt oxide (LiCoO2) for high energy density, lithium iron phosphate (LiFePO4) for improved safety, and lithium nickel manganese cobalt oxide (NMC) for a balance of performance characteristics.
l Recent advancements focus on enhancing cathode materials for higher energy density, longer cycle life, and reduced cost.
Anode Materials:
l Anode materials store lithium ions during charging and release them during discharging.
l Graphite is the most commonly used anode material due to its stability and relatively high lithium storage capacity.
l Silicon-based materials show promise for higher energy density but face challenges related to volume expansion and cycling stability.
Separator Materials:
l Separator materials provide a physical barrier between the cathode and anode, preventing short circuits while allowing the passage of lithium ions.
l Polyethylene (PE) and polypropylene (PP) separators are widely used due to their chemical inertness, mechanical strength, and porosity.
l Advanced separator technologies aim to improve safety by incorporating flame-retardant additives or developing self-healing properties.
The selection and quality of raw materials significantly impact the performance, safety, and cost-effectiveness of lithium batteries. Ongoing research and development efforts focus on optimizing raw material compositions, improving manufacturing processes, and enhancing battery performance to meet the growing demand for energy storage solutions in various applications.
Production Process
The production process of lithium batteries involves several intricate steps, starting from the preparation of electrode materials to the final assembly of battery cells.
Preparation of Electrode Materials:
1. Cathode Preparation:
l Cathode materials, such as lithium cobalt oxide (LiCoO2), lithium iron phosphate (LiFePO4), or lithium nickel manganese cobalt oxide (NMC), are mixed with conductive additives and binders.
l The mixture is then coated onto aluminum foil and dried to form a thin cathode film.
2. Anode Preparation:
l Anode materials, typically graphite or silicon-based compounds, are mixed with binders and coated onto copper foil.
l The coated foil is then dried to form the anode film.
Electrolyte Formulation:
l Electrolyte solutions are prepared by dissolving lithium salts, such as lithium hexafluorophosphate (LiPF6), in organic solvents like ethylene carbonate (EC) and dimethyl carbonate (DMC).
l The electrolyte solution must be carefully formulated to ensure optimal conductivity and stability while minimizing safety risks such as thermal runaway.
Assembly of Cells:
1. Stacking Electrodes:
l Cathode and anode foils are interleaved with separator sheets to form a jellyroll structure.
l This jellyroll structure is then wound tightly to maximize the active surface area within the battery cell.
2. Adding Electrolyte:
l The wound jellyroll is immersed or injected with the prepared electrolyte solution.
l The electrolyte permeates through the porous separator, facilitating the transport of lithium ions between the cathode and anode.
3. Sealing the Cell:
l The electrolyte-filled cell is sealed to prevent leakage and contamination.
l Sealing may involve heat-sealing techniques or the application of specialized adhesives.
Formation:
1. Initial Charging:
l The sealed battery cells undergo an initial charging process to activate the electrochemical reactions and stabilize the electrode-electrolyte interfaces.
l This step is crucial for achieving the desired capacity and performance characteristics of the battery.
2. Capacity Testing:
l After formation, battery cells undergo rigorous capacity testing to ensure uniform performance and quality control.
l Cells that fail to meet specified performance criteria may be rejected or subjected to further optimization processes.
Battery Packaging:
l Once formed and tested, individual battery cells are assembled into battery packs or modules, depending on the application.
l Battery packs may include additional components such as thermal management systems, safety features, and electronic monitoring circuitry.
l The assembled battery packs are then encased in protective housings and labeled for distribution and installation.
The production process of lithium batteries requires careful attention to detail at each stage, from the preparation of electrode materials to the final assembly of battery packs. Advanced manufacturing techniques and quality control measures are essential for ensuring consistent performance, safety, and reliability of lithium batteries across various applications.
Manufacturing Techniques
Manufacturers employ a variety of techniques to optimize the production of lithium batteries, aiming to improve efficiency, reduce costs, and enhance overall performance.
Solid-State Battery Production:
l Solid-state battery technology replaces liquid electrolytes with solid-state electrolytes, offering potential advantages in safety, energy density, and longevity.
l Manufacturing solid-state batteries involves specialized techniques such as thin-film deposition, sputtering, or atomic layer deposition to deposit thin layers of electrode and electrolyte materials onto solid substrates.
l Solid-state batteries require precise control over deposition processes and material interfaces to ensure uniformity and reliability.
Thin-Film Deposition Methods:
l Thin-film deposition methods, including physical vapor deposition (PVD) and chemical vapor deposition (CVD), enable the precise deposition of electrode and electrolyte materials onto substrates.
l PVD techniques, such as sputtering and evaporation, use physical processes to deposit thin layers of material onto a substrate surface.
l CVD techniques involve chemical reactions to deposit thin films from gaseous precursors, offering precise control over film composition and structure.
l Thin-film deposition methods are often used in the production of solid-state batteries, flexible batteries, and microbatteries for specialized applications.
Roll-to-Roll Manufacturing:
l Roll-to-roll (R2R) manufacturing enables high-throughput production of flexible and lightweight lithium batteries by continuously processing flexible substrates.
l In R2R manufacturing, electrode and electrolyte materials are coated onto flexible substrates, such as metal foils or polymer films, using roll-to-roll coating techniques.
l R2R processes offer scalability, cost-effectiveness, and flexibility in producing large-area batteries for applications such as wearable electronics, flexible displays, and printed electronics.
Additive Manufacturing (3D Printing):
l Additive manufacturing, or 3D printing, allows for the direct fabrication of complex battery structures with customizable geometries and compositions.
l 3D printing techniques, such as fused deposition modeling (FDM) and stereolithography (SLA), enable the rapid prototyping and production of battery components, including electrodes, electrolytes, and casings.
l Additive manufacturing offers opportunities for design optimization, material savings, and reduced manufacturing lead times, particularly for low-volume and custom battery applications.
Advanced manufacturing techniques play a crucial role in the production of lithium batteries, enabling the development of next-generation battery technologies with improved performance, safety, and versatility. From solid-state battery production to roll-to-roll manufacturing and additive manufacturing, these techniques contribute to the continued innovation and evolution of lithium battery technology for diverse applications.
Environmental and Safety Considerations
Lithium battery production must address significant environmental and safety concerns to ensure sustainable and safe manufacturing practices.
Waste Management:
1. Material Waste:
l During electrode preparation and cell assembly, excess materials may be generated as byproducts or waste.
l Manufacturers implement strategies to minimize material waste through efficient material utilization and recycling processes.
2. Chemical Waste:
l Chemicals used in electrode preparation and electrolyte formulation pose environmental risks if not properly managed.
l Recycling and treatment processes are employed to minimize chemical waste and mitigate environmental contamination.
Recycling Processes:
l Lithium battery recycling is essential for recovering valuable materials, reducing resource depletion, and minimizing environmental impact.
l Recycling processes involve disassembling battery packs, shredding, and sorting components to separate materials such as metals, plastics, and electrolytes.
l Recovered materials undergo purification and refining processes to prepare them for reuse in new battery production or other industries.
Safety Measures During Production:
1. Worker Safety:
l Manufacturers implement safety protocols to protect workers from exposure to hazardous chemicals and materials.
l Personal protective equipment (PPE), ventilation systems, and training programs are essential for ensuring worker safety.
2. Fire and Explosion Prevention:
l Lithium batteries pose risks of thermal runaway, fire, and explosion if mishandled or subjected to adverse conditions.
l Production facilities incorporate safety measures such as fire suppression systems, thermal monitoring, and emergency response protocols to mitigate these risks.
3. Environmental Impact Mitigation:
l Manufacturers must comply with environmental regulations and standards governing air and water emissions, waste disposal, and hazardous material handling.
l Environmental impact assessments and sustainability initiatives aim to minimize the carbon footprint and ecological footprint of lithium battery production.
Product End-of-Life Management:
l Proper end-of-life management is essential for mitigating the environmental impact of spent lithium batteries.
l Recycling programs, take-back initiatives, and regulations on battery disposal ensure responsible handling and recycling of end-of-life batteries.
l Designing batteries for easier disassembly and material recovery facilitates recycling and reduces landfill waste.
Environmental and safety considerations are integral to responsible lithium battery production. Implementing effective waste management, recycling processes, and safety measures ensures sustainable and safe manufacturing practices. By addressing these concerns, manufacturers contribute to the long-term viability and acceptance of lithium batteries as a key technology for energy storage and electrification.
Recent Developments and Innovations
Recent advancements in lithium battery technology have spurred innovations aimed at improving performance, safety, and sustainability across various aspects of production and application.
Advancements in Electrode Materials:
1. High-Energy Cathode Materials:
l Researchers continue to develop novel cathode materials with higher energy densities and improved cycling stability.
l Advancements include lithium-rich layered oxides, high-nickel content cathodes, and composite materials tailored for specific applications.
2. Anode Material Innovations:
l Silicon-based anode materials offer higher lithium storage capacities compared to graphite, albeit facing challenges related to volume expansion.
l Graphene and carbon nanotube additives improve the mechanical stability and conductivity of anode materials, enhancing overall battery performance.
Enhanced Manufacturing Techniques:
1. Solid-State Battery Production:
l Solid-state battery technology promises safer and higher energy density batteries by replacing liquid electrolytes with solid-state electrolytes.
l Advanced manufacturing techniques such as atomic layer deposition (ALD) and roll-to-roll processing enable scalable production of solid-state batteries with precise control over film thickness and composition.
2. Additive Manufacturing for Customization:
l Additive manufacturing, or 3D printing, allows for the rapid prototyping and customization of battery components with complex geometries.
l Innovations in additive manufacturing techniques enable the production of tailored battery designs for specific applications, including wearables, medical devices, and aerospace.
Environmental Sustainability Initiatives:
1. Recycling and Circular Economy:
l Industry initiatives focus on improving battery recycling technologies to recover valuable materials and minimize environmental impact.
l Closed-loop recycling processes aim to establish a circular economy for lithium batteries, where materials are recycled and reused in new battery production.
2. Green Manufacturing Practices:
l Manufacturers are adopting sustainable practices, such as renewable energy integration, water recycling, and reduced chemical usage, to minimize the environmental footprint of battery production.
l Life cycle assessments (LCAs) help identify opportunities for resource optimization and emissions reduction throughout the battery production process.
Safety and Reliability Enhancements:
1. Advanced Battery Management Systems (BMS):
l Next-generation BMS technologies incorporate advanced algorithms and sensors for real-time monitoring and thermal management of battery cells.
l Active safety features, such as cell balancing and temperature regulation, mitigate the risks of thermal runaway and improve battery reliability.
2. Materials and Design for Safety:
l Researchers explore materials and design strategies to enhance battery safety, including the development of flame-retardant electrolytes, self-healing separators, and robust cell enclosures.
Recent developments in lithium battery technology demonstrate a commitment to advancing performance, safety, and sustainability across the entire battery lifecycle. By leveraging innovations in electrode materials, manufacturing techniques, environmental sustainability initiatives, and safety enhancements, the industry is poised to address current challenges and unlock new opportunities for the widespread adoption of lithium batteries in diverse applications.
Applications and Market Trends
Lithium batteries have revolutionized numerous industries, driving innovation and enabling the widespread adoption of portable electronics, electric vehicles (EVs), renewable energy storage, and more. Understanding current applications and market trends provides valuable insights into the evolving landscape of lithium battery technology.
Consumer Electronics:
1. Smartphones and Tablets:
l Lithium batteries power the ubiquitous smartphones and tablets, providing long-lasting and rechargeable energy storage for portable devices.
l Demand for higher energy density batteries with fast-charging capabilities drives innovation in electrode materials and manufacturing techniques.
2. Laptops and Wearables:
l Lightweight and compact lithium batteries are essential for laptops, smartwatches, fitness trackers, and other wearables, supporting continuous usage throughout the day.
l Flexible and customizable battery designs cater to the evolving needs of wearable technology, enabling seamless integration into clothing and accessories.
Electric Vehicles (EVs):
1. Battery Electric Vehicles (BEVs):
l Lithium batteries are the primary energy storage solution for BEVs, offering long-range driving capabilities and fast-charging infrastructure.
l Advances in battery chemistry and manufacturing processes reduce costs, increase energy density, and extend the driving range of electric vehicles.
2. Hybrid and Plug-in Hybrid Vehicles (HEVs/PHEVs):
l HEVs and PHEVs utilize lithium batteries in combination with internal combustion engines to optimize fuel efficiency and reduce emissions.
l Battery advancements enable larger capacity and more efficient hybrid systems, enhancing overall vehicle performance and environmental sustainability.
Energy Storage Systems:
1. Grid-Scale Energy Storage:
l Lithium batteries play a crucial role in grid-scale energy storage systems, enabling the integration of renewable energy sources such as solar and wind into the power grid.
l Modular and scalable battery solutions provide grid stability, load leveling, and backup power during peak demand periods or grid outages.
2. Residential Energy Storage:
l Home energy storage solutions, such as lithium-ion battery packs coupled with solar photovoltaic (PV) systems, empower homeowners to reduce electricity costs and increase energy independence.
l Growing interest in residential energy storage drives market expansion, with manufacturers offering integrated battery solutions and smart energy management systems.
Aerospace and Military Applications:
1. Unmanned Aerial Vehicles (UAVs):
l Lithium batteries power UAVs, drones, and other unmanned aircraft, providing lightweight and high-energy density power sources for extended flight durations.
l Advancements in battery technology enable longer flight times, improved payload capacities, and enhanced mission capabilities for military and civilian applications.
2. Space Exploration:
l Lithium batteries are critical for space missions, providing reliable power sources for satellites, spacecraft, and rovers exploring planetary surfaces.
l Extreme temperature resistance, high energy density, and long cycle life are essential characteristics of space-grade lithium batteries.
Market Trends:
1. Rapid Growth and Adoption:
l The global lithium battery market continues to expand rapidly, driven by increasing demand for electric vehicles, renewable energy storage, and portable electronics.
l Technological advancements and economies of scale lead to cost reductions, making lithium batteries more accessible and competitive across various applications.
2. Diversification and Innovation:
l Market players diversify product offerings and invest in research and development to meet evolving customer demands and regulatory requirements.
l Innovation focuses on improving energy density, safety, sustainability, and recyclability of lithium batteries, driving market differentiation and competitive advantage.
Lithium batteries are ubiquitous across a wide range of applications, powering the transition to cleaner energy sources and driving technological innovation. Market trends reflect the growing demand for energy storage solutions that are efficient, reliable, and environmentally sustainable. Continued advancements in lithium battery technology will shape the future of transportation, energy infrastructure, and consumer electronics, paving the way for a more sustainable and electrified world.
Future Outlook
The future of lithium battery technology holds tremendous promise, driven by ongoing research, technological advancements, and shifting market dynamics. Key trends and developments point towards a future where lithium batteries play an even more significant role in shaping the energy landscape and powering diverse applications.
Emerging Technologies:
1. Solid-State Batteries:
l Solid-state battery technology holds the potential to revolutionize energy storage by replacing liquid electrolytes with solid-state electrolytes.
l Advantages include improved safety, higher energy density, and enhanced cycle life compared to traditional lithium-ion batteries.
2. Beyond Lithium Chemistries:
l Research into alternative battery chemistries, such as lithium-sulfur, lithium-air, and sodium-ion batteries, aims to overcome limitations of lithium-ion technology.
l These next-generation batteries offer higher energy densities, lower costs, and reduced environmental impact, opening up new possibilities for energy storage and transportation.
Sustainability and Environmental Impact:
1. Circular Economy and Recycling:
l The shift towards a circular economy model prioritizes the recycling and reuse of lithium battery materials, reducing reliance on finite resources and minimizing environmental impact.
l Advances in battery recycling technologies and infrastructure promote closed-loop systems, where materials are recovered and reintegrated into new battery production.
2. Green Manufacturing Practices:
l Manufacturers increasingly adopt sustainable production practices, incorporating renewable energy sources, minimizing waste generation, and optimizing resource utilization.
l Life cycle assessments (LCAs) and eco-design principles guide the development of environmentally friendly battery technologies from cradle to grave.
Integration with Renewable Energy:
1. Energy Storage and Grid Flexibility:
l Lithium batteries play a crucial role in supporting the integration of renewable energy sources such as solar and wind into the power grid.
l Energy storage systems provide grid stability, peak shaving, and backup power, enabling greater flexibility and resilience in the face of fluctuating renewable energy generation.
2. Decentralized Energy Systems:
l Distributed energy resources, combined with energy storage technologies, enable the development of decentralized energy systems that empower communities and reduce reliance on centralized power infrastructure.
l Smart grid technologies facilitate efficient management and optimization of distributed energy resources, enhancing reliability and grid resilience.
Electrification of Transportation:
1. Electric Vehicle Revolution:
l The electrification of transportation accelerates with the widespread adoption of electric vehicles powered by lithium batteries.
l Continued advancements in battery technology lead to longer range, faster charging, and lower costs, driving consumer acceptance and market growth.
2. Electrified Public Transit and Freight:
l Electrification extends beyond passenger vehicles to include public transit buses, commercial trucks, and freight vehicles, reducing emissions and dependence on fossil fuels.
l Investment in charging infrastructure and supportive policies spur the transition towards electrified transportation systems worldwide.
Market Expansion and Global Adoption:
1. Emerging Markets and Applications:
l Emerging markets, particularly in Asia-Pacific and Latin America, witness rapid growth in lithium battery adoption across diverse applications such as energy storage, electrified transportation, and consumer electronics.
l Technological innovation and falling costs make lithium batteries increasingly accessible and attractive for a wide range of industries and end-users.
2. Industry Collaboration and Partnerships:
l Collaboration between industry stakeholders, governments, research institutions, and academia fosters innovation, knowledge sharing, and the development of common standards and regulations.
l Strategic partnerships and alliances drive market expansion, facilitate technology transfer, and accelerate the commercialization of new battery technologies.
The future outlook for lithium battery technology is characterized by innovation, sustainability, and widespread adoption across diverse sectors. Emerging technologies such as solid-state batteries and alternative chemistries promise to overcome current limitations and unlock new opportunities for energy storage and electrification. As the industry continues to evolve, collaboration, investment, and strategic planning will be essential for realizing the full potential of lithium batteries in building a cleaner, more sustainable energy future.
Conclusion
In conclusion, the production of lithium batteries is a multifaceted process that encompasses raw material sourcing, intricate manufacturing techniques, and stringent environmental and safety considerations. As demand for efficient energy storage solutions continues to rise, understanding the complexities of lithium battery production is essential for driving innovation and sustainability in the energy sector.
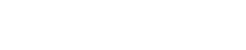